The Best Strategy To Use For Machine Nozzles
Spray nozzles are used to get rid of pollutants and also are important in the cleaning process of several producing processes. Kadant manufactures thousands of spray nozzles consisting of jet, fan, brush shower, disc follower, self-purging, trim squirt, and quick attach nozzles. Special tipped nozzles such as ruby and also cermet are additionally offered.
A clean thaw, without foreign fragments is needed for the hassle-free and also economical manufacturing of moulded components. Nearly all thermoplastics can be processed with the FN kind filter nozzle. Just PVC is not appropriate. By modifying the melt flow this nozzle has an extra benefit of a mixing impact which can improve homogenization.
The basic Herzog melt filter is based upon a perforated screen as this style has much less pressure decrease contrasted to various other filter types. This filter kind is suitable for filtering system fragments larger than 0.6 mm. The 2nd option is based upon a gap filter style which is made use of for filtering fragments smaller than 0.6 mm.
Any kind of international particles which are bigger than the holes or spaces are kept back in the guide duct. The filteringed system thaw circulations on via an outlet duct to the injection mould. Benefits of the filter nozzle kind FN: • Helps in reducing turn down rates because of tainted melt • Avoids mould as well as entrance obstructions due to international bodies in the melt • Assists protect the mould • Assists melt homogenization (blending effect) Technical Documents:Equipment filter nozzle type FN (display or gap filter).
Not known Details About Machine Nozzles
In today's international production setting, molders are seeking to enhance their injection molding procedures in every means feasible - machine nozzles. Different sorts of maker nozzles can help achieve that objective. Maker nozzles today can provide a selection of features, consisting of filtering, blending, and also shut-off of thaw flow. Decreasing the obstructing of gates and/or hot jogger ideas because of international product orcontamination in the melt stream with nozzle filters can conveniently improve uptime while additionally lessening damages to gates and hot-runner ideas.

Lastly, shut-off nozzles can decrease drool in molding procedures where the press is often disengaged from the mold, such as in many two-shot molding applications. MODULAR NOZZLE DESIGNS Maker nozzles are created to be easily threaded onto the injection molding barrel. This implies that the back end of each nozzle is customized to string onto the specific device barrel for which it is to be made use of.
Some device nozzles are of single-piece construction, which may cause much less expense initially. Various other nozzles are of modular style and building, which generally uses separate elements for the nozzle body, equipment interface, as well as mold and mildew interface. Modular layouts use a number advantages, the primary one being the capacity of a solitary nozzle body to interface with numerous shot barrels and also numerous mold and mildews.
Separate interfaces, each with the proper string requirements for the shot molding barrel that it is used on, can be connected to specific injection presses, each with an usual interface to the nozzle body. In this manner, the nozzle body might be after that be quickly fitted to every one of the different injection molding barrels made use of in a molding center.
The Main Principles Of Machine Nozzles
A modular maker nozzle design includes a modular pointer that can be conveniently exchanged, enabling the molder to have numerous suggestions to allow one nozzle to appropriately interface with multiple mold and mildews, each with different sprue-bushing specs. SCREEN-PACK NOZZLE FILTERS Nozzle filterings system capture contaminants in the melt stream to stop such bits from going into the mold and mildew and the shaped parts.


One of the most usual style is known as a screen pack (machine nozzles). It is composed of a metal disk perforated by a number of small openings, which is put along the internal diameter of the circulation network of the equipment nozzle. As the thaw passes with the flow network of the nozzle, it runs into the metal disk as well as is pressed through the small-diameter holes.
Advantages of a display pack are its straightforward design as well as low price. It is also relatively simple to size the diameters of the openings in the steel disk. There are several disadvantages to screen packs, too. The firstly drawback is that to guarantee the structural honesty of the steel disk versus the injection molding stress, the location of the solid steel will certainly be above the aggregate location of the small-diameter openings consisted of within the metal disk.
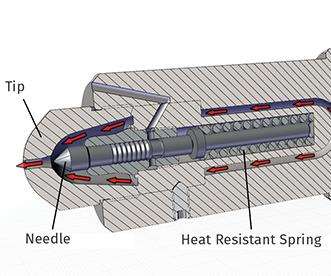
This leads to a recognizable and also substantial pressure decrease as the melt traverses through the display pack. This stress drop is big enough to affect the processing home window, and hence is inappropriate to many molders. The majority of molders will certainly not use screen packs or will certainly restrict their use to injection molding presses and/or mold and mildews where this kind of stress decrease is considered absolutely required.
The 6-Second Trick For Machine Nozzles
When a hole is blocked the reliable flow location of the thaw is lowered further, which leads to an additional increase in the pressure decline. As more pollutants are captured, the pressure decline remains to increase even additionally. Given the relatively tiny effective circulation area of the screen pack to begin with, each additional reduction in flow area has a visible further boost in pressure drop. machine nozzles.
At this factor, the display pack have to be cleansed, which exposes a 3rd disadvantage of this nozzle layout. To clean up the screen pack, the equipment nozzle need to be cooled down and dismantled so that the screen pack can be removed from the nozzle filter. The screen pack need to after that be cleaned up or changed.
When reconstructed, the maker nozzle can then be revived as much as the appropriate operating temperature level as well as molding might recommence. The entire process from shutdown of molding, through cooling down, disassembly, cleaning, reassembly, and heating up, may conveniently take a pair of hours or even more, depending upon the size of the machine nozzle.
additional info click this investigate this site